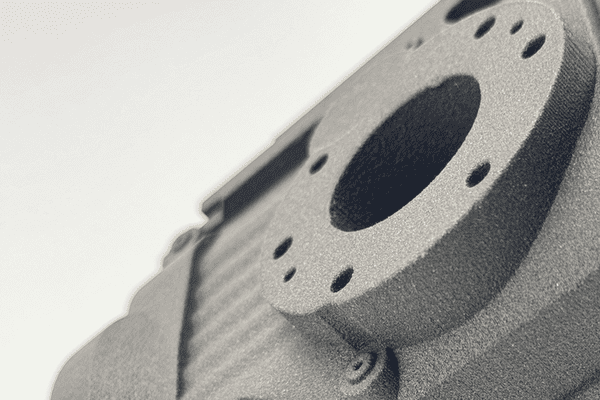
48 Hours/72 Hours/5 Days
380*380*284mm
± 300μm or 0.3%mm
23
Multi Jet Fusion (MJF 3D printing) is a powder bed fusion 3D printing technology developed by HP in 2014. It works by spreading a thin layer of nylon powder on a build platform, selectively fusing the powder using an inkjet array of heated nozzles, and adding an extra inkjet to refine details. This process is repeated layer by layer until the final part is created. MJF can create high-quality complex geometries and intricate parts without the need for support structures.
People are using MJF 3D printing for a variety of applications, from rapid prototyping to low-volume production runs, such as turbine components, brackets, hinges, rudder trim systems, drone frames, prosthetics, dental implant molds, watertight enclosures for electronics, and more.
MJF 3D printing, developed by HP, is a process that creates detailed and durable parts using a combination of inkjet printing and powder fusion. Here are what we do for MJF 3D printing processes at 3DSPRO:
1. MJF can create parts at a faster speed than other powder bed fusion 3D printing technologies.
2. MJF parts have excellent mechanical properties, including high tensile strength and durability.
3. MJF printed parts have consistent isotropic properties.
4. Compared to SLS, MJF delivers higher-resolution prints with finer feature details and smoother surfaces.
1. MJF primarily supports a limited range of materials, such as Nylon PA12, PA11, and TPU.
2. MJF parts typically have limited color options and often require dyeing to achieve desired colors.
3. The surface finish can still be rough and may require additional post-processing.
3DSPRO collect cookies on your computer to provide more personalized services to you. By using this website, you consent to the cookies we use and our Privacy Policy
Accept