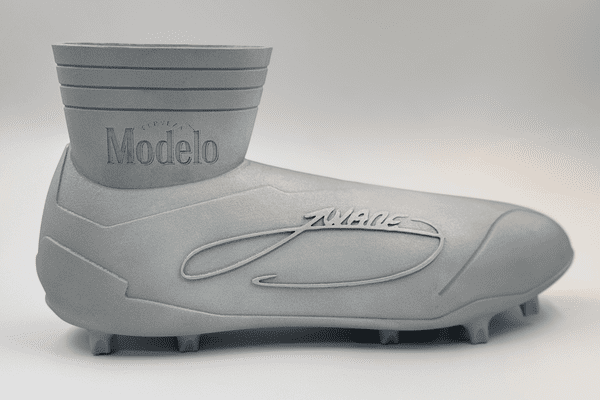
5 Days/7 Days
427*527*460mm
± 300μm or 0.3%mm
80
Selective Laser Melting (SLM) uses a high-powered laser to selectively melt metal powder and fuse it into a solid metal object. SLM is a powder bed fusion technology that involves laying a thin layer of metal powder on a build platform and selectively melting the powder with a laser according to the 3D design of the part. The process is repeated layer by layer until the metal part is complete.
SLM is widely used in various industries for the production of complex and high-strength metal parts. One of the most common applications of SLM is in the aerospace industry, where it is used to produce turbine blades, heat exchangers, structural parts, etc.
SLM 3D printing creates metal parts by melting and fusing metallic powder layer by layer using a high-power laser. Here are the processes of SLM 3D printing at 3DSPRO:
1. Allows for the creation of high-strength, complex metal parts with intricate geometries, such as manifold, internal channels, and undercuts.
2. A relatively fast process compared to other 3D printing technologies for metal parts.
3. Create parts with excellent mechanical properties and dimensional accuracy.
4. Has been widely used for applications in the aerospace, medical, automotive, and industrial manufacturing industries, etc.
1. May also produce parts with a rough surface finish (especially the printed side) that requires additional post-processing to achieve the desired surface quality.
2. SLM printers and materials are often expensive.
3. Require a high level of expertise to operate.
4. May produce parts with residual stresses and distortion in the final part, which can affect its mechanical properties and dimensional accuracy.
3DSPRO collect cookies on your computer to provide more personalized services to you. By using this website, you consent to the cookies we use and our Privacy Policy
Accept