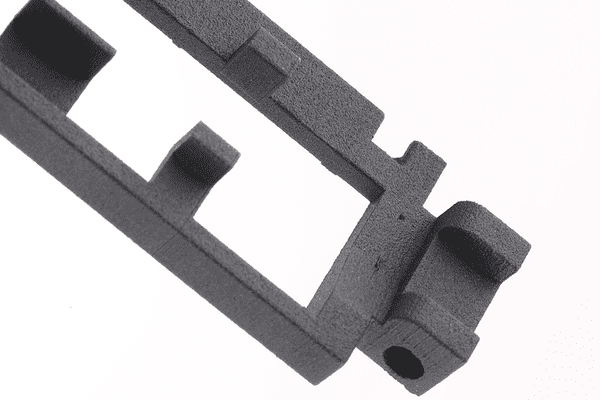
48 Hours/72 Hours/5 Days
550*550*850mm
± 300μm or 0.3%mm
28
Selective laser sintering (SLS 3D printing) uses lasers to melt and bond powdered materials selectively to form solid objects, one layer at a time. SLS 3D printing can create highly complex and intricate parts with detailed resolution without the need for support structures.
SLS is used in a wide variety of applications that require high-quality custom parts with good mechanical properties, such as commercial aircraft parts, medical implants, prosthetics, surgical tools, guides, automotive brackets, and housings.
SLS 3D printing creates objects by fusing powdered material layer by layer using a high-powered laser. Here are what we do for SLS 3D printing processes at 3DSPRO:
1. SLS can create highly complex and intricate parts with high accuracy and detail resolution without the need for support structures.
2. It works with a wide range of plastic materials, including nylons, PP, PC, and TPU, providing flexibility in applications.
3. Parts produced with SLS have excellent mechanical properties, including high strength and durability, suitable for functional prototypes and end-use products.
1. If you need your part to have a smooth surface, the original granular and rough finish of SLS 3D prints may not meet your needs.
2. The post-processing for SLS printed parts requires removing excess powder, and layer lines might affect the tolerance.
3. Flat surfaces may experience warping and distorting, and small holes may be clogged by the unsintered powder, affecting the accuracy and quality of the final product.
3DSPRO collect cookies on your computer to provide more personalized services to you. By using this website, you consent to the cookies we use and our Privacy Policy
Accept